CALCULATION OF THE BRINELL HARDNESS
Calculation formula for Brinell hardness:
For the Brinell hardness test, the selection of suitable test parameters is of decisive importance.
The Brinell method becomes inaccurate for very small or very large penetration depths. For this reason, the test load must be selected such that the following conditions are met for the mean indentation diameter:
0,24 * D < d <0,6 * D
In order to meet these conditions, 'Stress level B' was introduced. This depends on the material group to be tested.
The stress level is selected according to the following table:
STRESS LEVEL B FOR BRINELL HARDNESS TESTERS
|
Material
|
Stress level B [N/mm²]
|
Ball diameterD [mm]
|
Test forceF [N]
|
Recordable Hardness Range [HBW]
|
Steel and cast steel
Nickel and titanium alloys
Cast iron ≥ 140 HBW
Cu and Cu alloys ≥ 200 HBW
|
30
|
1 2,5 5 10
|
2,94,2 1839 7355 29420
|
95 – 650
|
Light metals and their alloys ≥ 35 HBW
|
15
|
1 2,5 5 10
|
- - - 14710
|
48 – 327
|
Cast iron < 140 HBW Cu and Cu alloys 350-200 HBW
|
10
|
1 2,5 5 10
|
98,07 612,9 2452 9807
|
32 – 218
|
Cu and Cu alloys < 35 HBW
Light metals and their alloys
≥ 35 < HBW < 80
|
5
|
1 2,5 5 10
|
49,03 306,5 1226 4903
|
16 – 109
|
Light metals and their alloys ≥ 35 HBW
|
2,5
|
1 2,5 5 10
|
24,52 153,2 612,9 2452
|
8 – 55
|
Lead and tin
|
1
|
1 2,5 5 10
|
9,807 61,29 245,2 98,7
|
3 – 22
|
According to DIN EN ISO 6506 Only ball diameters >1 mm may be used for testing cast iron
|
After the degree of stress has been determined, test load F and ball diameter D can be determined according to the table. In principle, the ball diameter should be as large as possible in order to cover as large and therefore representative a part of the sample surface as possible.
Hardness values determined with different ball diameters at the same degree of loading can only be compared to a limited extent. Hardness values determined with the same ball diameter but different degrees of loading are not comparable. Therefore, it is essential that all parameters are always specified when specifying a hardness value.
BRINELL HARDNESS TESTING RESULTS
According to DIN EN IS 6506-1 the result of a Brinell hardness test is indicated as follows:
310 HBW 2,5 / 187,2 / 20 ⇒ Hardness value as per Brinell
310 HBW 2,5 / 187,2 / 20 ⇒ Abbreviation for Brinell hardness
310 HBW 2,5 / 187,2 / 20 ⇒ Ball diameter in mm
310 HBW 2,5 / 187,2 / 20 ⇒ Test force [N] = 9.807 * test force specification
310 HBW 2,5 / 187,2 / 20 ⇒
Application time of the test force
(omitted if it is between 1-15 s)
FURTHER PREREQUISITES FOR BRINELL HARDNESS TESTING
More prerequisites need to be fulfilled for standard-compliant testing:
|
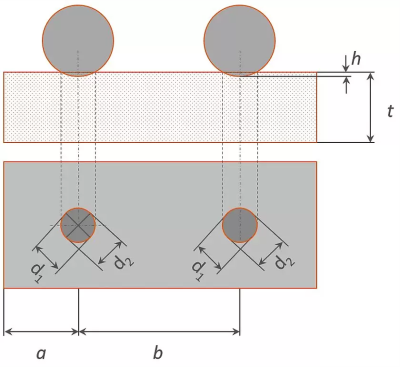
|
Test temperature
- normal requirements: 10°C bis 35°C
- high requirements: 23°C ± 5°C
Distances between the indentations and from the edge
|
|